Material renovável é opção para tornar a indústria mais sustentável
Por Suzel Tunes, da Pesquisa Fapesp | Apontado como um dos principais responsáveis pela emissão de gases de efeito estufa, que causam o aquecimento global, o setor de transportes busca formas de ser mais sustentável e investe em produtos e processos de menor impacto ambiental. A indústria automotiva tem usado uma alternativa que vem se consolidando em todo o mundo: o emprego de fibras naturais, de origem vegetal, na fabricação de peças e acessórios. Mais do que um simples fornecedor de matéria-prima, o Brasil é um dos centros de pesquisa e desenvolvimento dessa tecnologia.
Em agosto, a Universidade Estadual Paulista (Unesp) firmou convênio com a Volkswagen do Brasil para desenvolver novos compósitos que incluam em sua formulação fibras vegetais – compósitos são materiais formados por dois ou mais componentes, como vidro e metal, com propriedades superiores às que lhe deram origem. O objetivo é que esses novos materiais sejam utilizados em peças do acabamento interno dos automóveis da montadora.
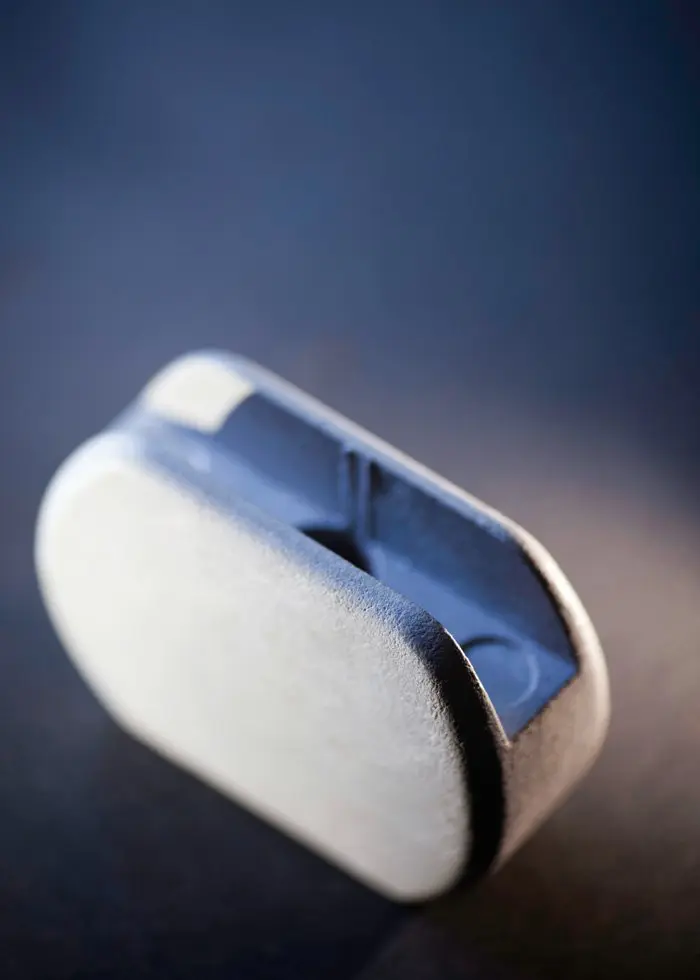
O projeto é liderado pelo engenheiro-agrônomo Alcides Lopes Leão e pela química Ivana Cesarino, coordenadores do Laboratório de Bioprocessos e Biotecnologia da Faculdade de Ciências Agronômicas da Unesp, em Botucatu (SP), e tem duração de 18 meses. Ao final do período, a multinacional espera contar com peças mais sustentáveis, em razão da redução do uso de plástico de origem fóssil em sua composição, e, sobretudo, com automóveis mais leves e eficientes do ponto de vista energético. A principal vantagem da substituição dos ingredientes minerais por fibras vegetais – materiais de menor densidade – é a redução do peso do veículo e, consequentemente, do consumo de combustível. Algumas limitações, contudo, ainda precisam ser superadas, como a baixa resistência das fibras naturais à umidade, a suscetibilidade a fungos e sua longevidade.
Leão estuda o uso de fibras vegetais em materiais compostos desde a década de 1990. A atual parceria com a Volkswagen é herdeira de um projeto financiado pela FAPESP em 2000 (ver Pesquisa FAPESP nº 104). Naquela época, Leão investigava o potencial da fibra de curauá (Ananas erectifolius), planta nativa da floresta amazônica que conhecera durante uma pescaria nos rios da região.
O projeto despertou o interesse da Volkswagen, que chegou a produzir algumas peças automotivas com a fibra, e o pesquisador foi convidado a ministrar palestras sobre o tema para os engenheiros da empresa no Brasil e na Alemanha. Mas a montadora não encontrou um fornecedor regular de curauá e engavetou o projeto. Passadas duas décadas, Leão foi surpreendido por um novo convite. “Eu já não tinha contato com ninguém da Volks. Eles decidiram investir na produção de peças com fibras vegetais e me localizaram este ano fazendo buscas na internet”, conta o pesquisador.
Agora, para definir a melhor fibra a ser incorporada ao plástico, estão sendo testadas quatro opções: coco, juta, sisal e bambu. Vai pesar na decisão a questão do abastecimento, que o pesquisador acredita estar mais bem equacionada. “Como o projeto atual tem alcance global, a Alemanha pode contar com fornecedores de fibras em diversos países”, considera. Inicialmente as fibras serão incorporadas ao polímero em escala macrométrica em seis peças que compõem o porta-malas do modelo Polo. Depois, a ideia é trabalhar na escala nanométrica. “A incorporação de nanocelulose dobra a resistência do compósito”, explica Leão.
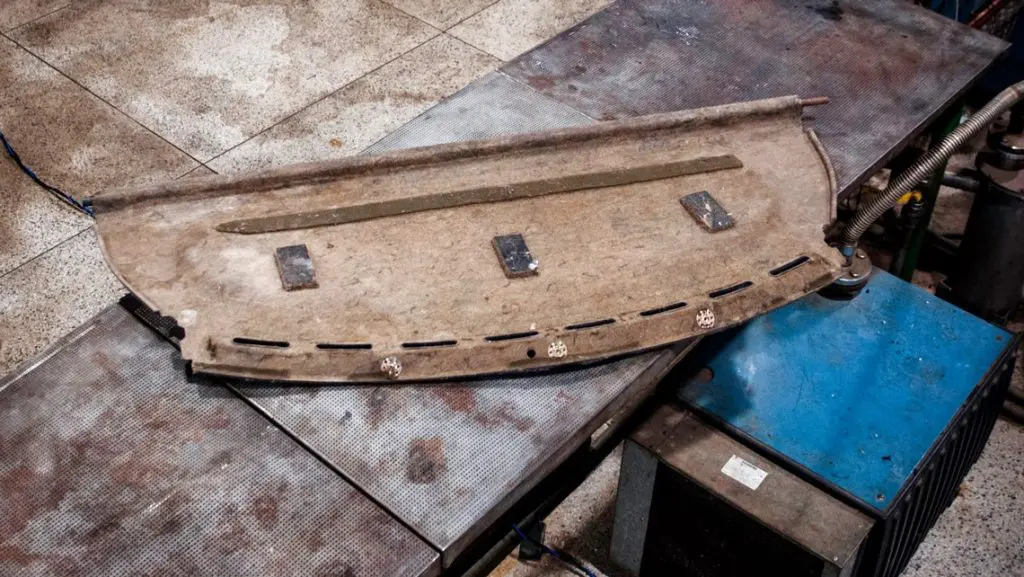
Segundo o pesquisador, as fibras naturais já são usadas em diferentes tipos de compósitos, em escala reduzida, por alguns fabricantes de automóveis no mundo. “A maior consumidora é a alemã Mercedes-Benz, que emprega por volta de 30 quilos de fibras por veículo. Na Volks, vamos começar com aproximadamente 8 quilos por veículo. Se pensar que ela fabrica 6 milhões de carros por ano, o volume pode vir a ser significativo”, diz. Nesses materiais compostos, o polímero funciona como a matriz, responsável por sua estrutura, e a fibra é o elemento de reforço. O uso sozinho da fibra para confeccionar peças automotivas não iria conferir a resistência de que o material necessita.
Desenvolver materiais de alta performance para a indústria automotiva a partir de matérias-primas regionais é também o propósito de uma equipe das universidades federais da Paraíba (UFPB) e de Campina Grande (UFCG) e do Instituto Fraunhofer para Tecnologia de Manufatura e Materiais Avançados, com sede em Bremen, na Alemanha. O projeto é financiado pela Fundação de Apoio à Pesquisa do Estado da Paraíba (Fapesq) e pelo Ministério da Educação e Pesquisa da Alemanha. No Brasil, é coordenado pela engenheira de materiais Renate Wellen, do Departamento de Engenharia de Materiais da UFPB.
Os pesquisadores começaram o projeto trabalhando com fibras de sisal, no Brasil, e linho, na Alemanha. “As melhores propriedades foram obtidas com o linho, que se molda melhor como tecido para ser incorporado ao compósito por compressão. O objetivo é utilizar o material na parte interna da porta, escolhida pela alta demanda
da indústria e por ser uma estrutura de menor complexidade”, revela Wellen.
Tal como no projeto da Unesp com a Volkswagen, a parceria entre brasileiros e alemães nasceu de buscas na internet. Dessa vez, foi o lado brasileiro que tomou a iniciativa. Empenhada em desenvolver projetos na área de fibras vegetais e sabendo do crescente interesse da Alemanha pela tecnologia verde, em 2015 a pesquisadora da UFPB fez contatos com diversas universidades e institutos de pesquisa germânicos.
Peças automotivas feitas com fibras vegetais são mais leves e resultam em menor consumo de combustível
Desses contatos resultou seu pós-doutorado no Instituto Fraunhofer de Tecnologia de Manufatura e Materiais Avançados de Bremen e o projeto atual. Para Wellen, coordenadora-geral de pesquisa da UFPB, a troca de experiência entre as equipes é um dos aspectos mais importantes do convênio. “Houve uma melhora na capacitação dos alunos. Temos dois integrantes da equipe fazendo doutorado na Alemanha.”
O novo polímero reforçado com fibras naturais está em fase de finalização e o protótipo de uma peça automotiva feita com ele foi apresentado em outubro na Feira K 2022, maior evento internacional da indústria de plásticos e borracha, realizado em Düsseldorf, na Alemanha. Já existe a perspectiva de desenvolvimento de um novo material compósito, possivelmente formulado com fibra de coco, matéria-prima abundante no Brasil. “Os alemães têm interesse em continuar a parceria”, diz Wellen.
Do carro de soja ao fibrocimento
A tentativa de utilizar fibras naturais no setor automotivo vem de longe. Em 1930, Henry Ford, pioneiro na produção automotiva em série, criou um material batizado de bioplástico. Sua composição exata é incerta, pois não se guardou registro da fórmula, mas em 1941 um protótipo produzido com o material ficou conhecido como Soybean Auto, carro de soja. O novo automóvel, contudo, nunca entrou na linha de produção da fábrica.
De acordo com informações do Benson Ford Research Center, instituto de pesquisa mantido pelo Henry Ford Museum, a eclosão da Segunda Guerra Mundial (1939-1945) suspendeu toda a produção de automóveis nos Estados Unidos. Com isso, o experimento do carro de soja não evoluiu. Depois, o esforço da empresa foi direcionado à recuperação das perdas causadas pela guerra e o automóvel de bioplástico caiu no esquecimento.
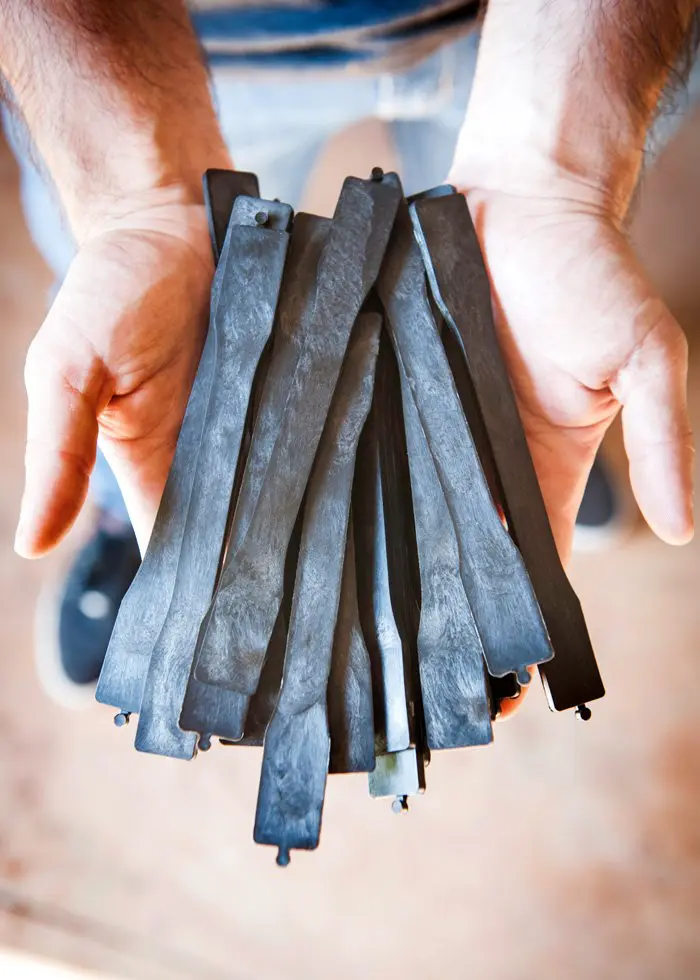
Para o engenheiro químico Sandro Amico, coordenador do Grupo de Materiais Compósitos e Nanocompósitos da Universidade Federal do Rio Grande do Sul (UFRGS), outro fator que contribuiu para o desinteresse da indústria foi o surgimento das fibras de vidro e carbono nas décadas de 1930 a 1950. Ele explica que as fibras sintéticas apresentavam vantagens como a elevada rigidez e a maior resistência mecânica a ataques químicos e ambientais – enquanto as naturais eram suscetíveis à umidade, por exemplo. Hoje, esse problema é contornável com o tratamento das fibras ou pelo uso de aditivos na formulação do compósito e a preocupação com o meio ambiente trouxe as fibras naturais de volta ao cenário industrial.
Amico trabalha há mais de duas décadas com diferentes tipos de fibra. “Hoje há vários exemplos de aplicações que até cinco anos atrás não existiam e outras que aumentaram de escala”, atesta o professor. Como exemplo, ele cita a madeira plástica conhecida como WPC (wood-polymer composite), que surgiu na década de 1960 e é formada por serragem de madeira e uma resina polimérica termoplástica, como o PVC ou polietileno. “Esse material tem feito grande sucesso comercial na América do Norte”, afirma.
Na Universidade Tecnológica Federal do Paraná (UTFPR), alunos do engenheiro florestal Ugo Leandro Belini, do Departamento de Desenho Industrial e da Pós-graduação em Sustentabilidade Ambiental Urbana, investigam como elaborar produtos mais sustentáveis, como luminárias e óculos. Um deles atraiu interesse de uma empresa local. “Em uma pesquisa de trabalho de conclusão de curso, foi criada uma armação de óculos a partir de um compósito de partículas de bagaço de cana-de-açúcar tingidas com um corante natural, açafrão, e aglutinadas com resina de poliuretano de mamona”, conta Belini.
Segundo uma análise de mercado publicada em 2020 pela consultoria norte-americana Grand View Research, o mercado de compósitos produzidos com fibra natural cresce no mundo todo. A empresa estima que o setor chegue a 2024 avaliado em US$ 10,9 bilhões. A área que mais emprega esses materiais é a da construção civil, que responde por mais da metade da demanda. No exterior, o material mais consumido é a madeira plástica WPC, utilizada em pisos, assoalhos, batentes de portas e janelas e revestimentos. As fibras também são usadas em elementos estruturais de concreto.
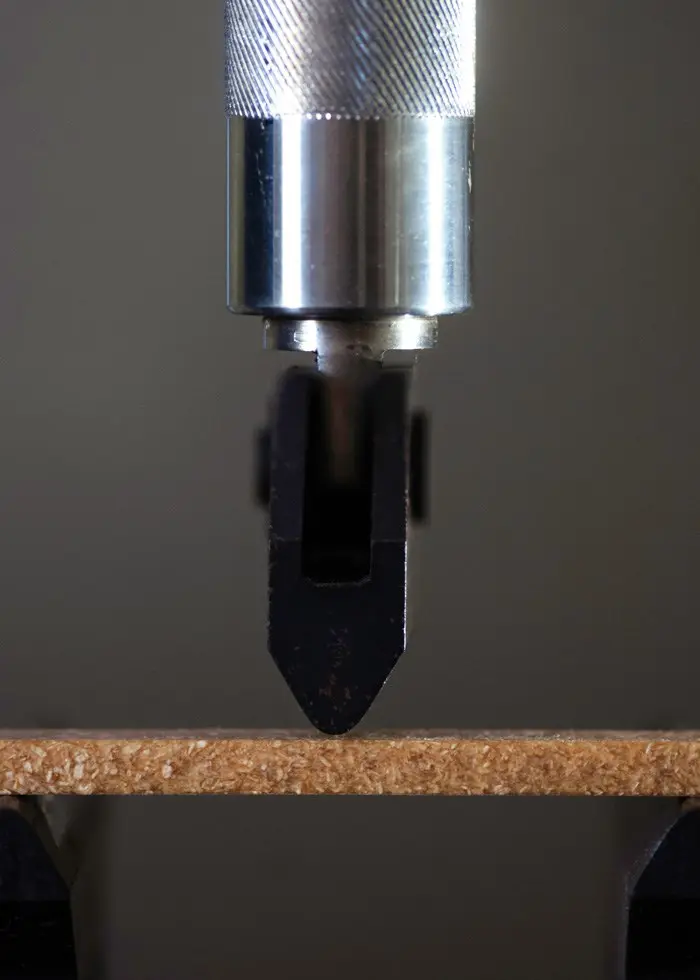
No Brasil, as telhas de fibrocimento feitas com uma mistura de cimento e amianto, fibra mineral reconhecidamente cancerígena, foram proibidas em 2017, abrindo espaço para novos compósitos de origem vegetal. Responsável pelo desenvolvimento de uma telha de fibrocimento fabricada com polpa celulósica patenteada em 2012, o engenheiro civil Holmer Savastano Junior, da Faculdade de Zootecnia e Engenharia de Alimentos da Universidade de São Paulo (FZEA-USP), lidera um projeto para a produção de placas cimentícias reforçadas por uma estrutura tridimensional (3D) de juta e malva.
Segundo o pesquisador, que desde os anos 1990 estuda o uso de fibras vegetais na produção de telhas (ver Pesquisa FAPESP no 98), as telas de tecido de juta e malva justapostas e conectadas entre si perpendicularmente formam uma estrutura que confere leveza com maior resistência mecânica e química do que o produto patenteado há 10 anos. O projeto recebe apoio da FAPESP e da Fundação de Amparo à Pesquisa do Estado do Amazonas (Fapeam), por meio de acordo de cooperação científica que reúne pesquisadores da USP e da Universidade Federal do Amazonas (Ufam).
“A equipe do Amazonas tem expertise em matrizes poliméricas e nós em camadas de fibrocimento. Há uma complementaridade e troca de experiências enriquecedoras”, diz Savastano. Com a proibição do uso de amianto, ele vê boas perspectivas de comercialização das novas placas. “Como não há mais risco de toxicidade, o fibrocimento tem sido considerado também para usos internos, em divisórias de ambientes, forros e placas de piso, o que pode elevar a demanda pelo novo produto no setor da construção.”
Este texto foi originalmente publicado pela Pesquisa Fapesp de acordo com a licença Creative Commons CC-BY-NC-ND. Leia o original. Este artigo não necessariamente representa a opinião do Portal eCycle.